Project X
Taylor Sweeney
Figure
Lighting / Electrical
Project X utilizes an uninterruptable power source system (UPS system) on top of the power supply. A UPS system is a battery that provides emergency power to the building should the main power input fail and generators are needed to supply the power to the building. The UPS system provides the needed power in the interim of the power failing and the generators starting up. The building has an incoming service of 18 megawatts, enough to power 18,000 homes, and 40,000 amps into the building. Underneath and throughout the entire building there is 26 miles worth of conduit use to transport electricity throughout the building. Located just outside of the building are 5 double-stacked generators that supply electricity to the building should the power fail for a significant amount of time.
Mechanical
The mechanical load for this building is very high. It is important to the owner and the owner’s tenants that the building be kept a consistent temperature so none of the equipment is overheated. To maintain temperatures throughout, the building utilizes multiple 550-ton centrifugal chillers and multiple 617-ton cooling towers. The building was built for a capacity of 8 chillers and towers, but only 3 where installed during this contract. The cooling towers and air-handling units are located on the roof, while the centrifugal chillers are located in the chiller room in the cellar. Each floor will have 8 computer room air handling units (CRAH) as well; there is also a 36,000 CFM air handler dedicated to support areas and computer room make-up air throughout the building.
Structural
The structural system for Project X is comprised of structural steel and cast-in-place concrete. Caissons and footings are used as the foundation system for the building, and are constructed with concrete and steel reinforcement; with the concrete have a strength of 3000 PSI. Each floor has a steel frame and bracing system with concrete slabs for the floors. The floors are slabs on metal decking and have a strength of 3500 PSI, and the deck is 3” 20 gauge composite deck. The structure for this building is unique in the sense that building is only 4 floors about ground with a cellar below, but it actually stand the height of an 8 story building. For the bridges between this building and the existing building on site are constructed from steel, with an architectural grade steel finish, that is fully welded and ground smooth. In Figure 2 above you can see the foundation for the cellar along with some of the electrical conduit.
Fire Protection
The fire protection system is a pre-action water based fire suppression system. The system includes a hybrid system of both dry and wet sprinklers. This system was selected due to the nature of the building, where accidental activation of the sprinkler could cause untold damage to the building. In rooms without ceilings installed upright sprinklers were installed. Rooms with a suspended ceiling in place have dry pendant sprinklers. This system has pre-action sprinkler heads that will activate once the given locations reach 155 degrees.
Transportation
Firgure 1
Moving throughout the building is very easy. With the building have 4 floors and a cellar there is a need for two elevator shafts and two stair cases. With the core of the building being utilized as rentable space, the elevators and stair cases are located along the perimeter of the building, as seen in figure 2.

Firgure 2
Security
Due to the nature of the building security was very important not only to the owners but to the clients renting the space. To accommodate the needs for the building a high end security system was installed. The system is comprised of both video cameras that monitor each floor as well as limited access throughout the building granted buy swipe access. Card readers are located at each door to ensure only those allowed to access the given rooms can enter the space. The building security system also has biometric readers for areas that are more restricted.
The construction of Project X took place in just over 18 months. The critical task to this project were the installation of the roof as well as the the trim out of the MEP work. The project started off with minimal amount of demolition because there were no existing buildings in the location of Project X, and very few existing conditions. With excavation being completed sheeting and shoring had to be put in place to retain the earth, this was done with a soldier pile and lagging system that can be seen in figure 1. Once the excavation of the site was complete caissons and footings were installed. Once the structure began being built three cranes were brought to site. These cranes located on the west, south, and east sides of the site were vital to the steel erection process as well as the installation of the mechanical equipment on the roof. Once the mechanical system was installed and the building was into the enclosure phase the cranes were removed from site.
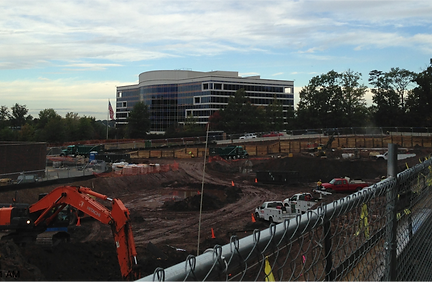
Building Statistics II
Construction
Sustainability Features
VA2 was originally projected to receive a LEED Silver certification, but was actually awarded a LEED Gold certification as well as being Energy Star rated. The LEED certification was based on U.S. Green Building Council’s (USGBC) “LEED 2009 for Core and Shell Development”. The main aspects that aided this project to becoming LEED Gold Certified include but are not limited to:
-
-Integration of recycled building materials
-
-Use of regional materials
-
-Low-emitting materials
-
-Construction waste management

Figure 3: Roof Detail
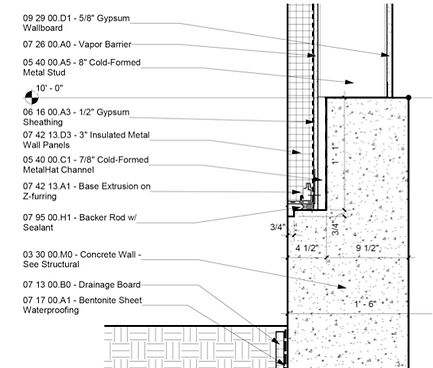

Figure 1: Wall Connection Detail
Figure 2: Building Façade
Architecture
The design of the building is a four story steel building, sitting on top of a single floor cellar. Caissons as well as the foundation of the cellar support the building. The skeleton of the building consists of a steel structural system with concrete slabs for flooring. Each of the four floors is currently in the process of being fitted out for the demands of the occupants renting the space. With each floor used as a rental space, the roof holds much of the mechanical equipment. The layout of each floor is very open, there is a corridor running around the perimeter of each floor, with the center left entirely open for future fit-outs.
Codes
VA2 is classified as a Group B, Type IIB, under the International Building Code (IBC) of 2009. VA2 is also regulated by various statewide codes pertaining to electrical, mechanical, and plumbing codes. Additional codes referenced include:
-
-National Fire Protection Act
-
-Americans with Disabilities Act
Zoning
Zoning of the building is requirement dictated by the local county. This building is in an undisclosed location.
Historical Requirements
There are no historical requirements to take into consideration for this project.
Building Enclosure
Building Façade
The building façade is consistent around the entire building. VA2 is cladded with insulated metal panels and aluminum storefront curtain wall as seen as Figures 1 and 2. The insulated metal panels are zinc-coated galvanized steel sheets. The curtain walls have aluminum sunshades that have photovoltaic panels that produce 15 watts at peak performance
Roofing
VA2 utilizes a low-sloped roof system. The roof is a thermoplastic polyolefin material on top of a 1 ½” steel deck filled with concrete and rigid insulation. Since the roof has a slight slope, there is a drainage system to ensure that there isn’t rainwater ponding.
EXP US Services, Inc.
Bohlery Engineering
Building Statistics I
General Building Data

Undisclosed by Owner Request
Building Name
Undisclosed by Owner Request
Project Location
158,000 SF
Building Occupants
Undisclosed by Owner Request
Size (Square Feet)
5 June 2013
Number of Floors
4 Floors
Project Start Date
GMP
Project Completion
5 December 2014
Project Delivery Method
Building Cost
$39 million
Project Team
Forrester Construction Company
Owner
Undisclosed by Owner Request
General Contractor

Architect
Environetics

MEP Engineer
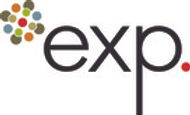
Civil Engineer
